Patient-centred, Planet-friendly: The propellant-free, metal-free design solution changing what’s possible in drug delivery devices
The real cost of medication nonadherence
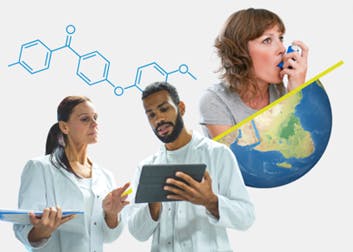
Approximately 50% of adults and 8% of children globally have a chronic condition1 requiring medical treatment. It’s estimated that 125,000 preventable deaths occur in the U.S. annually2 – deaths caused by patients failing to take medications correctly.
However, medication nonadherence not only costs lives, it also places a huge burden on healthcare systems. With an estimated 50-60% nonadherence,2 approximate associated annual costs range from $290 billion in the U.S, to €1.25 billion in Europe and $7 billion in Australia1.
As well as the impact medication nonadherence has on patients and healthcare, the disposable drug delivery devices used to combat it also have a negative effect on the environment due to their high product carbon footprint (PCF).
The team at research-driven pharmaceutical company Boehringer Ingelheim wanted to change that – developing a solution that not only improves patient outcomes, but also protects the world they live in.
Solutions, limitations and issues
From the commercial availability of nebulisers in 1930s, to the introduction of hydrofluoroalkane (HFA) pressurised metered-dose inhalers (pMDIs) in 1990s, drug inhalation therapy has led to considerable improvements in the treatment of chronic respiratory conditions. However, each delivery solution comes with its own limitations and issues – from ease-of-use, to efficacy, to environmental impact.
Let’s take pMDIs, approximately 9/10 of the medication dose delivered by standard pMDIs is deposited in the oropharynx, with only 10%–15% inhaled into the lungs3. In addition, pMDIs also require slow and controlled inhalation – and adequate patient coordination – for optimal drug deposition. And although HFA-pMDIs improve lung deposition – by reducing both velocity and particle size –they still require good patient coordination and slow inhalation, and the propellant has 1,000 times the global warming potential of carbon dioxide4.
Dry-powder inhalers (DPIs) remove the need for such propellants, they are breath-actuated, using the process of inspiration to inhale, disperse and deposit the medication in the lungs. They result in a 95% reduction in CO2 emissions when compared to MDIs4. However, DPIs require a high inspiratory flow rate – which is difficult to use by certain patient groups – and are also associated with high oropharyngeal deposition and sensitivity to moisture which negatively impacts the performance of the device.
A need for change
Understanding the issues with existing delivery solutions and driven by a need for change, the team at Boehringer Ingelheim challenged themselves with three core aims. (1) avoid propellants while reducing requirements for patient coordination and inspiratory effort (2) optimise drug delivery to the lungs (3) improve the patients’ experience of taking their inhaled medication5.
The result – the propellant-free, portable, pocket-sized Respimat® Soft Mist™ Inhaler (SMI) – a category defining inhaler that uses a mechanically powered tension spring rather than propellant to generate a slow moving, long-lasting mist that enables easy inhalation5.
By forcing a metered dose of drug solution through the precisely engineered innovative uniblock nozzle, the device produces two fine jets of liquid that converge at a pre-set angle. The collision of these two jets generates the unique soft mist that ensures patients receive a consistent and reliable dose every time – a true game-changer in drug delivery devices.
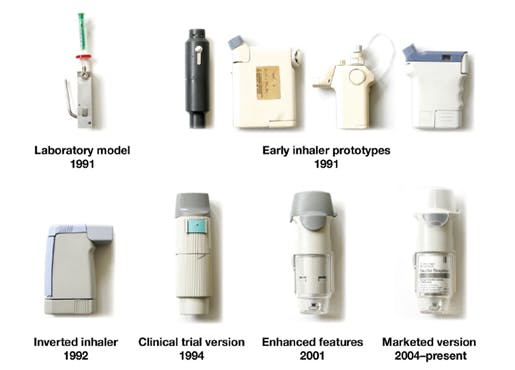
Change never stops
However, once the category had been defined, the team didn’t rest. Understanding that change never stops and committed to providing benefits beyond treatment, they moved to enhance the revolutionary Respimat® Soft Mist™ Inhaler – by maintaining its usability and efficiency whilst reducing its environmental impact by making it re-usable.
To achieve this new goal, it became clear they needed to overhaul the materials used within the device.
A partner for change
Searching for a metal-free alternative to reduce manufacturing inefficiencies, the team approached Victrex. The challenge – to provide a solution that enabled more design freedom and easier processing through moulding for mass production for very small parts to reduce the manufacturing costs per unit from machining.
Finding ways to improve a device or to develop new solutions is challenging – but with the right high performing materials, that journey can be easier. Victrex helped the team discover what is possible, and how far they could push the boundaries when inventing with PEEK.
Material Solution
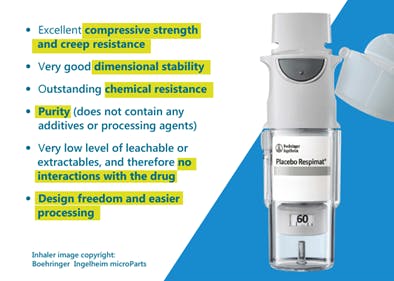
VICTREX™ PEEK is known to be one of the highest performing polymers in the world. What makes this material unique is its multi-faceted features. VICTREX™ PEEK was selected as the material of choice due to its excellent compressive strength and creep resistance, dimensional stability, outstanding chemical resistance, purity, very low level of leachable or extractables, and design freedom.
A major consideration in material selection was ease of processing to enhance and streamline the production process – reducing time and costs while increasing output. The economies of scale gained by PEEK’s ability to be mass produced via injection moulding (vs. machining of metal parts) helps allow the production of sufficient device units to meet the wider demographic and volume of patient capable of being served by SMIs.
To further enhance the performance of the material for this unique set of requirements, Victrex worked with the Boehringer Ingelheim team to develop a customer specific polymer grade, to align with the narrowed tolerances within specifications.
A game-changing solution
All of this culminated in Respimat® re-usable, an enhanced SMI significantly reducing waste and PCF. In contrast to most disposable plastic inhaler devices needing to be replaced after initial medication runs out, Respimat® re-usable can use up to six medication refill cartridges – a feature that is estimated could lead to 1.2 million fewer inhalers being sent to landfill each year in the UK alone6 – making Respimat® re-usable 71% better for the environment than the previous disposable version6.
And the innovation continues, with the 2nd generation product moving from single use inhaler to the multi-use and into the new practice area of equine veterinary care – continuously improving and evolving.
As drug delivery parts and assemblies get thinner and smaller, the need for strong materials, such as PEEK, are selected due to its high-performance, semi-crystalline mechanical strength, outstanding chemical resistance, and dimensional stability across a broad temperature range. PEEK is a material that many medical and drug delivery device OEMs reach for.
Let’s make change
Victrex has more than 40 years’ experience working with pioneering manufacturers to identify and calculate the potential benefits and value of replacing existing materials and parts with polymer alternatives – helping OEMs from various industries identify the technologies and solutions that they need to adopt in order to realise their vision.
Collaborating for over 10 years, Boehringer Ingelheim and Victrex continue to push and change what’s possible in drug delivery devices – refining materials to ensure minimised waste, improved melt filtration and purity. Working together, we have the vision, the tools and the products to support moves away from inefficient dated solutions and towards more effective sustainable alternatives, helping to improve patient outcomes and protect the environment. Let’s make change.
You may also want to read...
Drug delivery devices: How everyone wins when patient compliance is achieved (victrex.com)
Drug delivery devices: 3 key factors to consider for material selection (victrex.com)
References:
1. BMJ Open (January 21, 2018) Economic impact of medication non-adherence by disease groups: a systematic review. https://bmjopen.bmj.com/content/8/1/e016982
2. McKinsey& Company (August 23, 2017) A 360-degree approach to patient adherence. https://www.mckinsey.com/industries/life-sciences/our-insights/a-360-degree-approach-to-patient-adherence3. National Library of Medicine (September, 2006) Use of Respimat® Soft Mist™ Inhaler in COPD patients. https://www.ncbi.nlm.nih.gov/pmc/articles/PMC2707154
4. The Commonwealth Fund (May 16, 2023) A Hidden Contributor to Climate Change — Asthma Inhalers. https://www.commonwealthfund.org/blog/2023/hidden-contributor-climate-change-asthma-inhalers
5. Springer (April 6, 2017) The Respimat® Development Story: Patient-Centered Innovation. https://link.springer.com/article/10.1007/s41030-017-0040-8
6. Nursing Times (September 17, 2019) NHS seeks to reduce carbon footprint with new reusable inhalers. https://www.nursingtimes.net/news/respiratory/nhs-seeks-reduce-carbon-footprint-new-reusable-inhalers-17-09-2019
7. “Evolution of the Respimat® inhaler design” image is from the article “The Respimat Development Story: Patient-Centered Innovation” by Herbert Wachtel . Sabine Kattenbeck . Stephen Dunne and Bernd Dissea. This article is distributed under the terms of the Creative Commons Attribution-NonCommercial 4.0 International License (https://creativecommons.org/licenses/by-nc/4.0/)
About the author
Marcus Jarman-Smith, Head of Marketing - Medical
Marcus joined Victrex in 2006 and has held technical roles with Victrex's medical business unit (Invibio) and commercial roles in Business Development, scouting for breakthrough technologies as well as supporting the development of Victrex's Additive Manufacturing offering. Marcus holds a PhD in chemical engineering, tissue engineering and biomaterials from the University of Bath, in the UK. Marcus's expertise is in PEEK in medical and dental applications as well as food contact, materials and technologies for Additive Manufacturing and 3D printing. Marcus has been appointed as Head of Marketing for Medical as of February, 2024.
About the author
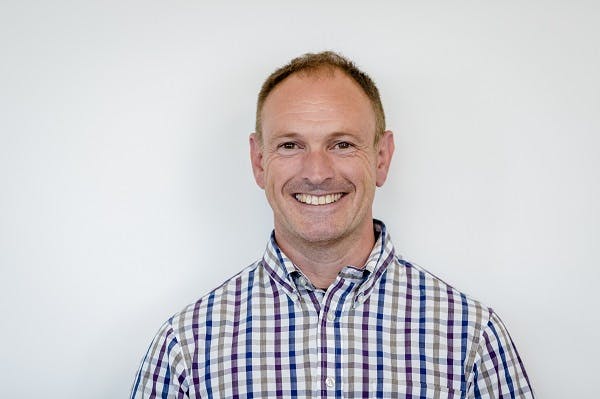