PEEK (polyetheretherketone) vs PAEK (polyaryletherketone) Polymers: Understanding key differences and applications
With the introduction of new PAEKs (PolyArylEtherKetones) such as VICTREX AE™ 250 unidirectional tape for breakthrough performance in aerospace composites and, more recently, VICTREX AM™ 200 filament that redefines Z-direction strength in additive manufacturing, I'm often asked, " Is that PEEK?" and "What's the difference between PEEK and PAEK?" Time for an explanation!
The easiest is to think of the term "PAEK" as a family name - it describes the general family of polymers consisting of at least aryl, ether and ketone building blocks, as I mentioned in an earlier blog.
You may be surprised to hear that over 340 different PAEKs are reported to date, but most of these are amorphous and of little industrial interest.

At Victrex, we prefer to focus on semi-crystalline materials, because this ensures polymers with good chemical resistance, fatigue, creep and wear properties, as I’ve discussed previously.
The best-known PAEK is PEEK, and its repeat unit looks like this:
Other PAEKs that Victrex manufactures include VICTREX HT™, which is PEK:
And VICTREX ST™, which is PEKEKK:
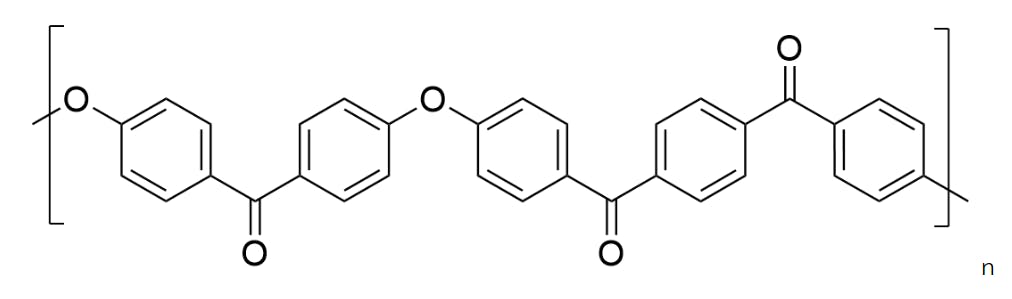
As the ratio of ketone-to-ether increases, so does the glass transition temperature (Tg) and the melting point (Tm).
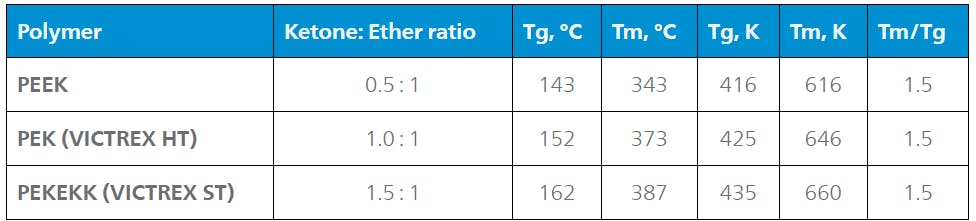
Need help selecting the right polymer for your temperature requirements?
Browse our PEEK polymer specifications to compare thermal properties across our complete product range.
A higher Tg can be desirable for applications requiring higher stiffness and strength at higher temperatures because this is the temperature above which the polymer changes from being stiff and glassy to being softer and more rubbery.
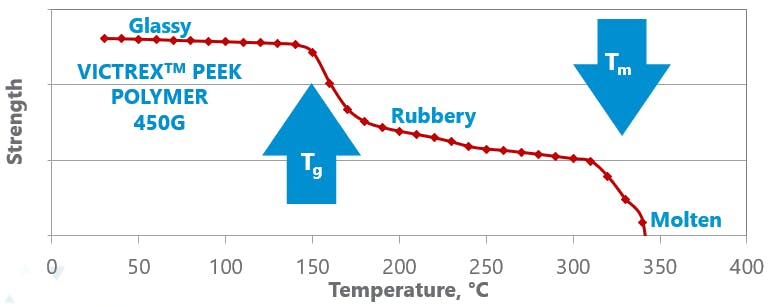
However, there’s a compromise here because a higher Tm means that the polymer must be processed at a higher temperature which can be challenging. Typically, PAEKs are processed at temperatures 30 – 60°C above their Tm and realistically, it can become tricky to process thermoplastics much above 430°C.
Looking at the table above, there’s something really interesting going on: I’ve included Tg and Tm measured on the Absolute or Kelvin temperature scale, K (in case you’re wondering, K = °C + 273.15). When we look at the ratio of Tm-to-Tg based on the Kelvin scale, we can see that there is a constant ratio of 1.5 : 1 between them, and this is a kind of “unwritten rule” in what we call semi-crystalline all-para PAEKs.
Re-inventing the rules At Victrex, we asked ourselves, “wouldn’t it be great if we could break this rule? Then we could lower the Tm without lowering the Tg, offering our customers a lower processing temperature whilst maintaining high temperature performance.”
This was the idea which ultimately led to the PAEKs we call LMPAEKs, used in VICTREX AE™ 250 UD tape and VICTREX AM™ 200 filament. These polymers typically have a lower Tm:Tg ratio of 1.35, and that means a Tm and a processing temperature reduced by ~40°C but a Tg that is at least as good as PEEK’s.
In LMPAEK™ Explained and why it’s suited to composites and additive manufacturing we’ll explore some additional features and benefits of these unique VICTREX LMPAEK co-polymers which makes them ideally suited to composites, hybrid over-moulding and additive manufacturing.
© Victrex plc. 2021. All rights reserved.
Disclaimer
About the authors
John Grasmeder, Chief scientist at Victrex
Dr John Grasmeder has over 25 years’ experience in the polymer industry, in R&D, commercial and business leadership positions at ICI, BASF, Hoechst and Shell joint ventures in both the UK and Germany. He has been with Victrex since 2005 and was Technical Director from 2010. He became Chief Scientist in 2016.