Top 10 PEEK Polymer F&Qs: AI answers to your most asked questions
ChatGPT is an Artificial Intelligence chatbot created by OpenAI and launched in November 2022. It was trained on a massive dataset of text to generate human-like responses to prompts. We asked ChatGPT “what are the Top 10 questions about PEEK polymers?”. Our Chief Scientist. Dr. John Grasmeder gives his answers:
What is PEEK and what are its properties?
PolyEtherEtherKetone (PEEK) is one of the world's highest performing thermoplastics used in engineering applications. It supports multiple performance requirements, including excellent mechanical, chemical resistance retained at extreme temperatures. Compared to metals, PEEK-based materials are very light weight, easily shaped, resistant to corrosion and can have considerably higher specific strength (strength per unit weight).
What are the applications of PEEK?
PEEK is a semi-crystalline polymer and therefore it is used widely in bearing and wear applications and in applications requiring chemical and fatigue resistance, such as downhole in wells the oil & gas industry, in gears and thrust washers in machinery & automotive applications, and brackets in airplanes. PEEK polymer-based solutions can also be found in consumer electronics applications such as smartphones, home appliances and medical devices.
Is PEEK a thermoplastic or a thermoset?
PEEK polymer is capable of being processed on conventional thermoplastic equipment. Granules are generally recommended for injection moulding, extrusion, monofilament and wire coating operations. Powder is used for compression moulding whilst fine powders are generally used for coating processes and composite pre-preg manufacture.
What is the difference between PEEK and other engineering plastics?
PEEK has a unique combination of desirable properties, chief among these being high temperature performance, wear, and chemical resistance – it is a good “all rounder” – which sets it apart from other polymers. Other polymers tend to have 1 or 2 particular strengths, whereas PEEK has several. This means that most application for PEEK are focused on replacing metals rather than other polymers.
What is the melting temperature of PEEK?
The melting temperature of PEEK is 343°C (649°F). This high melting temperature makes PEEK suitable for high-temperature applications where other polymers would degrade or melt.
Is PEEK biocompatible?
Yes. PEEK-OPTIMATM polymer has biocompatibility in conformance with ISO 10993-1 for use in the manufacture of medical devices for implantable and non-implantable applications.
What is the maximum continuous operating temperature for PEEK?
PEEK is suitable for continuous-use temperatures up to 260°C (500°F) according to the Relative Thermal Index classification in UL 764B. Looking at the PAEK family more generally, commercially available PAEKs have glass transition temperatures up to 170°C (338°F).
Can PEEK be used in high-stress applications?
All materials have their limitations but generally, PEEK, being regarded as one of the highest performing thermoplastics can indeed tolerate stresses higher than other polymers can. Due to its excellent fatigue resistance, PEEK is especially suited to applications where cyclic, repeated stresses are encountered.
What is the impact resistance of PEEK?
That depends upon how one measures impact resistance! Below its Tg of 143°C, PEEK is a glassy polymer but is one of the tougher glassy polymers.
Can PEEK be recycled?
As a thermoplastic, parts, components or scrap PEEK can be readily chopped or ground, remelted and reprocessed – extruded or moulded for example – into something new. In our laboratories, we have successfully reground, remoulded and retested PEEK several times with no loss of strength detected. In addition, as a valuable material, there are many companies which specialize in recovering, recycling and reprocessing PEEK.
For over 40 years, VICTREX™ PEEK products have proven their performance in very demanding environments. Today, the Victrex portfolio includes PEEK resins, powders and compounds as well as forms and parts such as filaments, film, rods, sheets, UD-tapes or composite plates in selected areas.
About the author
John Grasmeder, Chief scientist at Victrex
Dr John Grasmeder has over 25 years’ experience in the polymer industry, in R&D, commercial and business leadership positions at ICI, BASF, Hoechst and Shell joint ventures in both the UK and Germany. He has been with Victrex since 2005 and was Technical Director from 2010. He became Chief Scientist in 2016.
450G™ PEEK
About the author
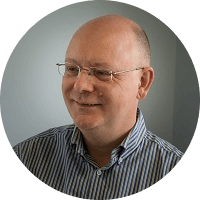