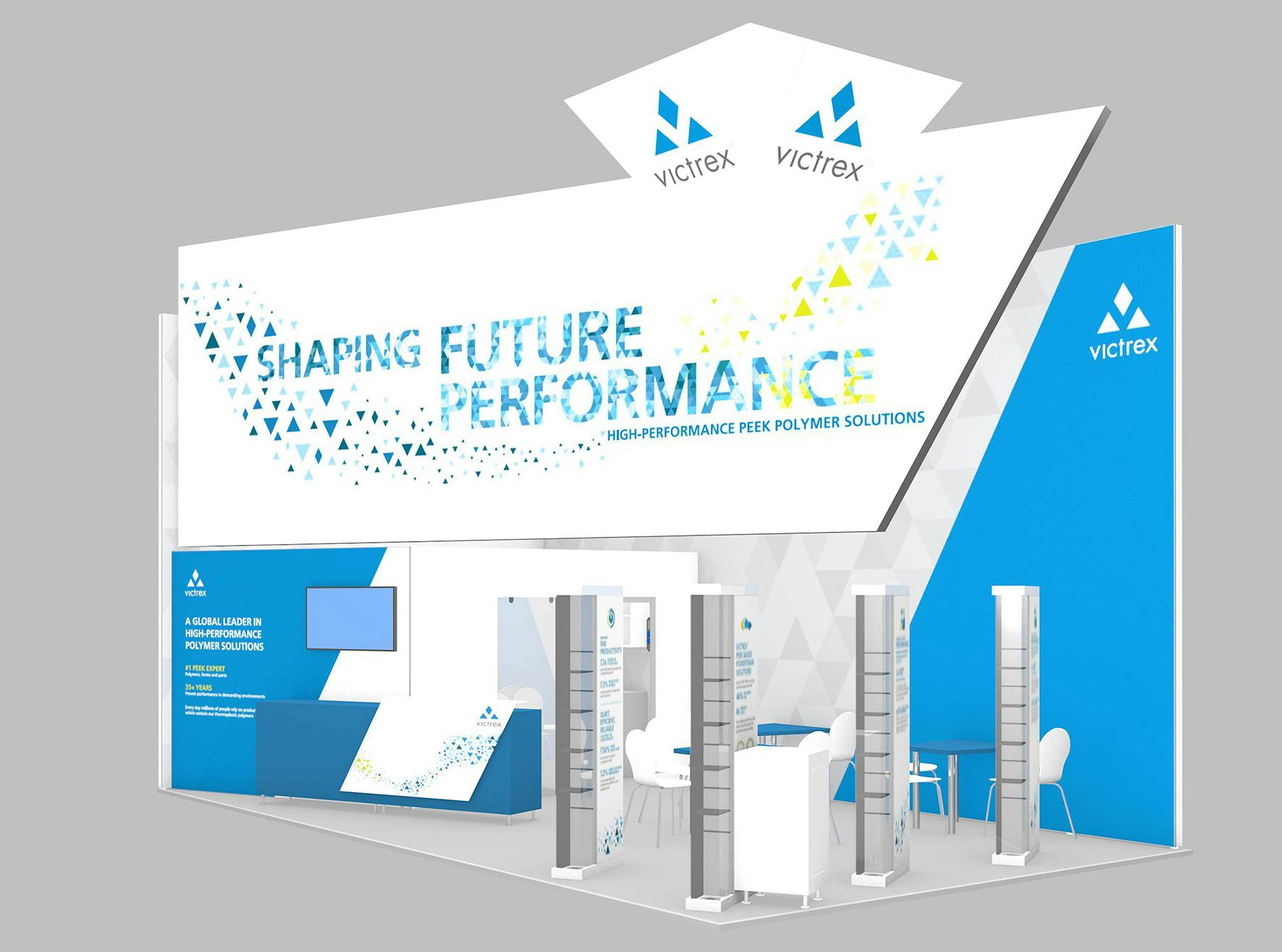
Auf der Messe Fakuma stellt der weltweit führende PAEK1-Experte Victrex erneut unter Beweis, dass das Unternehmen weit mehr ist als „nur“ ein Hersteller von Hochleistungspolymeren. Ein neues, umfangreiches Food-Grade-Portfolio, eine neuartige Lösung für Elektromotoren und für Zahnräder für die Automobilindustrie, Impeller für elektronische Haushaltsgeräte, Investitionen in den Aufbau einer Lieferkette für den Einsatz thermoplastischer Composite-Bauteile in der Luftfahrtindustrie und Partnerschaften bei der Entwicklung neuer PAEK-Produkte für die additive Fertigung – sie alle sind stellvertretend Beispiele dafür, das Victrex weitergehende Lösungen auf der Basis der VICTREX™ PAEK-Polymere vorantreibt. Dazu zählen in ausgewählten Bereichen auch Bauteile wie Composite-Befestigungsklemmen für den Flugzeugbau. Grundlage für diesen beeindruckenden Erfolgskatalog ist die Erfindung und Entwicklung von PEEK vor 40 Jahren und das Engagement von Victrex, das sich auf PAEK-/PEEK-Thermoplaste konzentriert.
Die Begriffe „Innovator“ und „Lösungsanbieter“ scheinen gegenwärtig etwas abgenutzt; dennoch beschreiben sie exakt Portfolio und Services von Victrex auf Basis der leistungsstarken Polyaryletherketone (PAEK), auf die sich das Unternehmen seit seiner Gründung konzentriert hat. Heute kommen Thermoplaste dieser Polymerfamilie und insbesondere VICTREX™ PEEK in unzähligen Anwendungen zum Einsatz, etwa in den Bereichen Automobilbau, Elektronik, Energie, Fertigung und Maschinen- bzw. Flugzeugbau sowie in der Medizin.
Lebensmittel- und Getränkeindustrie: Anwendungen mit dem neuen VICTREX FG-Portfolio
Auf der Fakuma stellt Victrex ein spezielles PEEK-Food-Grade-Portfolio vor, das Herstellern helfen soll, den strengen gesetzlichen Vorgaben und Qualitätsanforderungen in der Lebensmittelindustrie gerecht zu werden. Im Vergleich zu Metallen bietet die neue „VICTREX FG™“-Familie von Hochleistungsthermoplasten Herstellern zusätzliche Vorteile bei Wirtschaftlichkeit, Produktivität sowie Leistungsfähigkeit und erfüllt die Erwartung von Verbrauchern nach Geschmacksneutralität. Das Anwendungsspektrum reicht von Kochgeschirr und Getränkespendern für den gewerblichen und privaten Gebrauch bis hin zu industriellen Anwendungen wie Komponenten mit Lebensmittelkontakt in Fördersystemen, in aseptischen Prozessen, in Sensoren, Zahnrädern und Düsen. Weitere Einblicke gewährt ein Vortrag im Aussteller-Forum der Messe: „3 Things to Consider for Reliable, Regulatory-Compliant Food Applications” (Mittwoch 17. Oktober 2018, 15:40 bis 16:20 Uhr, Konferenzzentrum West, Raum Paris).
Elektronische Geräte: Leichtere und langlebigere Staubsaugerkomponenten mit verbesserter Lebensdauer ermöglichen Geräuschreduktion und höhere Energieeffizienz
Bei Haushaltsgeräten erlaubt das Hochleistungspolymer Designern, neue Ansätze für die Entwicklung kleinerer, aber leistungsstarker Staubsaugerkomponenten zu erforschen. Beeindruckend ist dabei, dass VICTREX PEEK im Spritzgussverfahren die Fertigung von sehr präzisen Bauteilen, die hohe Drehzahlen meistern können in einigen Fällen schneller als 100.000 U/min (zum Vergleich: Strahltriebwerke drehen nur mit 15.000 U/min) , ermöglicht, während sich Geräusche um bis 50 Prozent reduzieren lassen. Zudem erlaubt das günstige Verhältnis von Steifigkeit zu Gewicht des Materials, dass der Impeller bei diesen hohen Geschwindigkeiten seine Form beibehält und zu einer stärkeren Saugwirkung im Vergleich zu weicheren Materialien führen kann. Dient das Polymer als Ersatz gefräster metallischer Komponenten, können Bauteile mit geringerem Gewicht gefertigt werden und somit die Motorgröße und Anzahl der benötigten Einzelteile reduzieren. Außerdem widersteht VICTREX PEEK einer Vielzahl von Haushaltschemikalien sowie Hitze und Feuchtigkeit. Im Vergleich zu der zerspanenden Fertigung von Metallen kann das Spritzgussverfahren zu potenziellen Kosteneinsparungen für die Hersteller beitragen und ermöglicht zudem die schnelle Umsetzung neuer Designs, Verkürzung der Produkteinführungszeit und schnellere sowie weniger kapitalintensive Steigerung der Produktion.
E-Motoren im Automobilbau: Beenden APTIV™ Folien die Suche nach dem idealen Nutisolationsmaterial?
Während die Automobilindustrie zu Elektrofahrzeugen übergeht, ist die Suche nach effizienteren E-Motoren mit hoher Leistungsdichte und niedrigeren Kosten noch im Gange. Die meisten Motorenhersteller haben sich für den Einsatz von Permanentmagnet-Synchronmotoren (PMSM) entschieden, da dieser Motortyp im Vergleich zu anderen E-Motortypen einen höheren Wirkungsgrad hat und zugleich weniger (Bau-)Raum benötigt. Da PMSM bei Temperaturen, die die Isolationen schädigen können, abschalten, ist das Wärmemanagement ein entscheidender Leistungsfaktor für E-Motoren in Fahrzeugen die Entwicklung des Isolationssystems steht damit im unmittelbaren Zusammenhang.
Beim Forschen nach dem idealen Nutprofil-Isolator führten die Victrex-Ingenieure eine Simulation durch, bei der als Nutisolationsmaterial ein 250 Mikrometer starkes Meta-Aramid-PET-Laminat durch eine 150 Mikrometer dünne, auf PEEK basierende APTIV™ Folie ersetzt wurde. In der Simulation wurde so eine um 40 Prozent dünnere und dazu wärmeleitfähigere thermoplastische Nutisolationsfolie verwendet und aufgezeigt, wie der Wärmefluss von den Drahtwicklungen zum Stator und dem äußeren Kühlwassermantel verbessert werden kann. Weitere Simulationen zeigten die hervorragende Wärmeleitfähigkeit der APTIV™ Folie. Diese ermöglicht ein verbessertes Wärmemanagement und um zwei bis drei Grad Celsius niedrigere Temperaturspitzen bei den Drahtwicklungen im Vergleich zu herkömmlichen Laminaten und trägt dazu bei, den E-Motor kühl zu halten. Bei verbessertem Wärmemanagement und der dünneren Nutisolation konnte in den Simulationen potenziell die Kupferdichte (d. h. der Nut-Füllfaktor) um zwei Prozent erhöht werden. Schließlich ergab dies einen Anstieg des kontinuierlichen Antriebsdrehmoments von fünf Prozent, was zu höherer Leistungsausbeute bei gleicher Motorengröße führen könnte.
Gut gerüstet mit PEEK-Polymeren in Antriebssystemen
In der Automobilindustrie wird VICTREX PEEK bereits häufig in Antriebskomponenten wie Dichtringen, Anlaufscheiben, Buchsen und Lagern eingesetzt, während das Polymer als Metallersatz bei Zahnrädern in anspruchsvollen Antriebsanwendungen eher als ein unwahrscheinlicher Kandidat gilt. Jedoch werden mit kleineren und verkleinerten Motoren „Geräusch, Vibration und rauer Lauf“ (Noise, Vibration, Harshness – NVH) heute zu einer der größten Herausforderungen für OEMs und Zulieferer. Zahnradlösungen von Victrex haben gezeigt, dass sie in der Lage sind, Rasseln und Heulen bei Motoranwendungen um bis zu 50 Prozent (3 dB) zu reduzieren. Gewicht und Trägheitsmoment sind zudem bei Zahnrädern aus VICTREX HPG™ wesentlich geringer als bei Getrieben aus Sintermetall, was zu einer höheren Systemeffizienz beiträgt.
Zukunftsweisende Composite-Lösungen für die Luftfahrt
Auf der Fakuma präsentiert Victrex außerdem eine Vielzahl von auf VICTREX™ PAEK basierenden Composites und umspritzter Hybridbauteile für den Einsatz in der Luftfahrtindustrie. Das Unternehmen arbeitet derzeit gemeinsam mit Kunden daran, Zykluszeiten durch kontinuierliche Fertigungsprozesse auf wenige Minuten zu reduzieren. Anders als die noch heute häufig verwendeten Duroplaste, bei denen Zykluszeiten durchaus in Stunden gemessen werden, tragen thermoplastische Verbundwerkstoffe entscheidend zur Steigerung der Produktionsraten im Flugzeugbau bei. Um die Technologiereife für den Serieneinsatz zu erlangen und die etablierte Lieferkette im Aufbau zu unterstützen, hat Victrex mit dem langjährigen Entwicklungspartner Tri-Mack Manufacturing in das Joint Venture TxV Aero Composites investiert. Davon sollen alle Verarbeiter profitieren, die das Potenzial des Hybrid-Overmoulding-Verfahrens erkannt haben und in die Technologie investieren.
PEEK wird 40: die Gründe für den Erfolg des noch jungen Hochleistungspolymers
Die inerten Eigenschaften der vielseitigen PAEK-Polymere sind ein Hauptgrund für deren Erfolg. Die Polymerfamilie ist ideal für extreme und anspruchsvolle Umgebungen geeignet. Während alternative Materialien spezifischen Anforderungen gerecht werden, können die an der Spitze der Polymerpyramide stehenden PAEKs und PEEKs gleich mehrere Anforderungen auf einmal erfüllen. Ihre Eigenschaften umfassen geringes Gewicht, hohe Festigkeit und hohe Beständigkeit gegen Verschleiß, Temperatur, Ermüdung und aggressive Flüssigkeiten und Chemikalien. Zusammen können sie zu verbesserter Kraftstoffeffizienz, verlängerter Lebensdauer von Bauteilen, größerem Komfort (Laufruhe, weniger Lärm), mehr Gestaltungsfreiheit und höherer Kosteneffizienz beitragen.
Ein weiterer wichtiger Grund für den Erfolg ist, dass sich Victrex strategisch auf diese besondere Familie der PAEK-Hochleistungspolymere konzentriert. In der Folge konnten in den zurückliegenden vier Jahrzehnten durch wegweisende Materialentwicklungen, strategische Entscheidungen und die enge Zusammenarbeit mit den Kunden viele Meilensteine erreicht und diese Erfolge weiterentwickelt werden. Victrex setzt mit seinen PAEK- und PEEK-Lösungen seinen Weg fort, die Leistungen von morgen zu prägen. Das beharrliche Engagement für Innovation und Erfolg wird auch das zentrale Thema des Unternehmens auf der Fakuma sein (Halle A4 – Stand 4106) und einen ersten Vorgeschmack auf den 40. Geburtstag von PEEK im November geben.
1) Polyaryletherketone (PAEK) sind eine Familie von Hochleistungsthermoplasten, zu denen z. B. das Polyetheretherketon (PEEK) zählt.